HVAF “Flash-Carbide” as alternative to Electroplated Hard Chrome
Thermal spray coatings in general, and HVOF sprayed tungsten carbide coatings in particular, were able to replace Electroplated Hard Chrome (EHC) only in a small segment of the industry. The major reason, stalling further acceptance of HVOF coatings is their high cost compared to EHC, and specifically when addressing thin EHC coatings (“flash-chrome”), typically applied to thickness of only 15 to 30 micron (.0006” to .0015”).
The thickness of “flash-chrome” requires a small amount of material to be applied and needs a short time for processing. Besides, 15-30 micron EHC allows meeting many parts tolerances requirements without grinding, using surface buffing/polishing only when required. Those factors provide very competitive cost for flash chrome, which is the main reason that industry continues using it regardless of growing regulatory restrictions worldwide. The perfect examples of such applications are hydraulic rods, pistons, plungers, shafts, rolls, and tooling used in heavy machinery, automotive, aerospace, medical applications, etc.
A single and the most important factor, driving the cost of an HVOF coating, is the cost of spray material. For years, the focus of the HVOF cost improving developments was on using cheaper spray powders and on increasing the deposit efficiency (DE) of the process. However, the most important reason for high spray material cost in the HVOF coating is the need to apply very thick coatings as compared to EHC, and the need to grind a substantial part of this coating off to meet dimensional and roughness requirements of the coated part. The typical HVOF coating thickness after finishing is 100-250 microns (.004” to -010”), and another 125-150 microns are over-sprayed for grinding.
The main reason for the application of such thick HVOF coatings is the use of relatively coarse spray particles, typically 10-45-micron (.0004” to .0016”) particle size distributions. Smaller particles are heavily overheated in a typical HVOF process, resulting in oxidation of the metal matrix and the decomposition of carbides, making the coating too brittle for the majority of service conditions.
- To provide reliable surface coverage and reasonably low level of through porosity, 4-5 layers of particles must be applied. Considering that the average size of the spray particles is 30 microns and some deformation during spraying, the 4-5 layers would end up with about a 100-micron coating thickness.
- With such a coarse spray particle size, the typical surface roughness is about Ra 3.0 microns. The surface has to be ground, and additional coating thickness has to be applied for finishing to size and specified surface roughness.
- The additional coating thickness is also related to rather high absolute thickness deviation when targeting a 200-micron as-sprayed layer (10% deviation is already +/- 20 microns).
HVAF Flash Carbide
Due to a low temperature of combustion, the HVAF process is able of depositing fine particles of WC-based materials without their oxidation and thermal deterioration. The spray particles of 5-15 microns (.0002″ to .0006″) and 2-10 micron (.00008″ to .0004″) sizes are routinely used in HVAF applications.
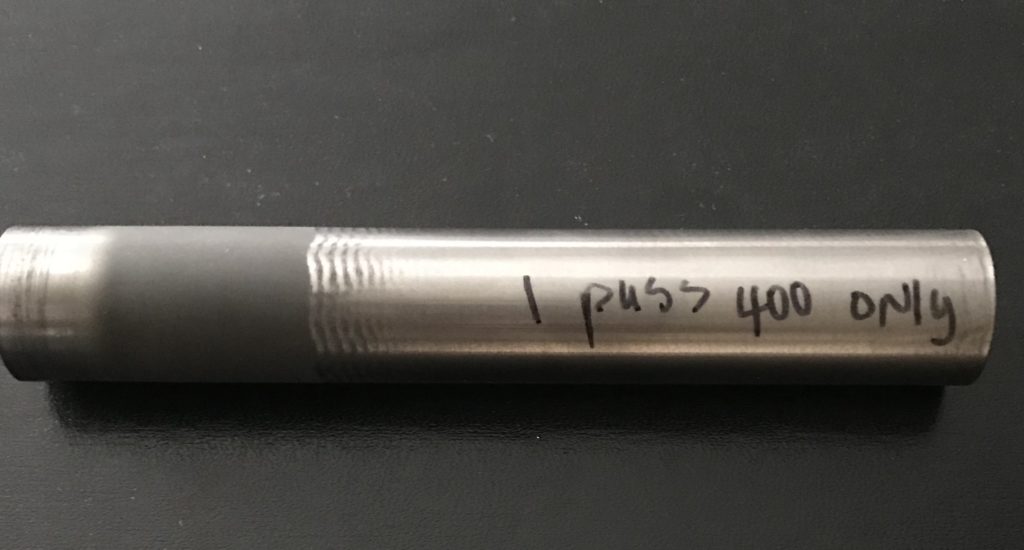
Utilizing very fine and dense WC-10Co-4Cr spray particles, the HVAF process demonstrates the ability to apply non-permeable to gas, coatings at a thickness well below 50 microns, achieving a surface roughness Ra 1.5-1.6 microns when spraying on a ground or polished steel substrates (no grit blasting). Without additional grinding, the as-sprayed surface is belt-polished to Ra 0.14 microns, while removing less than 9 microns of coating thickness, measured from the tops of the initial surface roughness. Thus, there is a real possibility to create a technology, based on the same principles as used in a flash-chrome coating: application of 25+/- 3-micron coating thickness with low surface roughness, which will meet the finished part tolerances without grinding. If needed, the surface roughness is brought down to required level by polishing only. The resulting cost of spray material becomes comparable with EHC. Costly and time consuming grinding operation is eliminated. Considering that the HVAF spray rates exceed HVOF process by five times and that 35 microns coating thickness is routinely applied with only one pass with HVAF, the total cost of the HVAF “flash- carbide” coating would be 10-fold lower than typical HVOF coatings, i.e. well comparable to the cost of “flash-chrome.”
Article written by A. Verstak edited by R. McDemus