HVOF (High Velocity Oxygen Fuel)
The HVOF process (High Velocity Oxygen Fuel process) is best know for its use with applying carbides. Thermal Spray operators use the HVOF process to apply Tungsten Carbide/cobalt alloys and chrome carbide coatings.
With the HVOF process, the combustion of the gases is contained inside the torch itself. The expanding gases rapidly accelerate out the front of the torch. The speed of the gases and the carbide particles both exceed the speed of sound. This can seen by the shock diamonds on the flame itself. The shock diamonds are common in afterburners and are the evidence that it is exceeding the speed of sound.
The Most Cost Effective Complete HVOF System Available
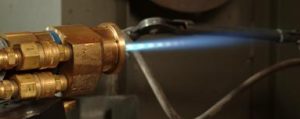
HVOF Process Flame
Note the shock patterns in the HVOF process flame
Mobile HipoJet 2700 HVOF System
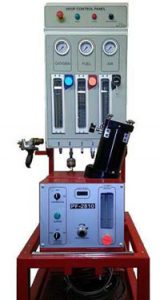
Complete portable HVOF system, HipoJet 2700
A complete HipoJet 2700 includes the HVOF gun, HVOF gas flow panel, gas regulators, flash back arrestors, PF 700 powder feeder, gas control module, and a mobile cart. This compact system is easily moved to alternate locations.
Increase Profits with a low maintenance HVOF gun
HipoJet 2700 HVOF Gun
The HipoJet 2700 HVOF gun design utilizes an internal axial-feed powder injection. Specially designed gas mixing and combustion chambers allow for high thermal efficiency and maximum particle heating, unrestricted gas and powder flow. The resulting HVOF process creates high particle velocities and dense, low oxide coatings. All hose connections enter the gun axially, producing a streamlined and compact unit. The versatile gun body design allows for quick maintenance operations. A variety of gun mounts for machine and robot mounting are also available
PF 2810 Powder Feeder
Reliable rotating disk with simple low-cost maintenance
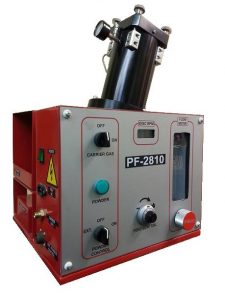
PF 2810 Powder Feeder
The model PF-700 operates on a volumetric feed principle. Slots in the powder wheel at the base of the canister fill with powder. Rotation of the powder wheel forces the powder into the exit ports. An inert carrier gas transports the powder from the exit ports through the powder hose and to the thermal spray gun. This system is built to withstand the spray environment. The PF-700 holds 700 CC of powder, the weight of which will vary depending on the material being sprayed.
HipoJet 2700 with Hybrid Attachment
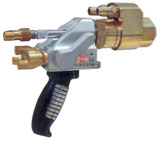
HipoJet 2700 with Hybrid
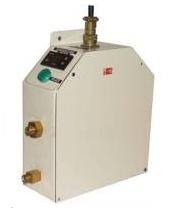
Water Jam Box
The optional hybrid attachment is used when the absolutely densest coating is required. The water cooled front end allows the melted particles to remain in the high-velocity stream longer thus accelerating them to a higher velocity.
An HVOF system uses a combustible gas mixed with oxygen to create a flame inside of the spray gun at a temperature of approximately 5500°F. The resulting gasses of combustion expand rapidly and can only exit out the nozzle of the gun resulting in a gas stream speed that exceeds the sound barrier. A sonic boom with aftershock diamond patterns is the evidence of this phenomena.
This is the heat source to melt and accelerate the material to be sprayed. The material to be sprayed is in the form of a powder that is fed into the center of the flame where it is melted. Once it is melted in the flame, the liquid metal is atomized and accelerated to a high velocity from a combination of the pressure from the flame and compressed air that is injected around the flame.
The atomized molten metal now forms a columned stream, similar in appearance to a spray paint pattern, except this is molten metal. The molten stream of metal is deposited on the component to be coated at a thickness of .0005″ (.0127mm) per pass to .002″ (.0254 mm) per pass. The variation of thickness per pass is depended on the material being sprayed and the amount of heat build up on the part being coated. This system is especially good for depositing tungsten carbide and chrome carbide. Check our prices, we are far more cost effective than a JP 5000, Diamond Jet, or a Jet Kote.